У діяльності бюро діагностування ремонтних підрозділів металургійних підприємств балансування робочих коліс димососів і вентиляторів у власних підшипниках виконується досить часто. Ефективність даної регулювальної операції, значна в порівнянні з малими змінами, внесеними в механізм. Це дозволяє визначити балансування як одну з низьковитратних технологій при експлуатації механічного встаткування. Доцільність будь-якої технічної операції визначається економічною ефективністю, в основі якої лежить технічний ефект від проведеної операції або можливі збитки від несвоєчасності проведення даного впливу.
Виготовлення робочого колеса на машинобудівному підприємстві не завжди є гарантією якості зрівноважування. У багатьох випадках підприємства-виготовлювачі обмежуються статичним зрівноважуванням. Зрівноважування на балансувальних верстатах, безумовно, є необхідною технологічною операцією при виготовленні й після ремонту робочого колеса. Однак, неможливо наблизити виробничі умови експлуатації (ступінь анізотропності опор, демпфірування, вплив технологічних параметрів, якість складання й монтажу й ряд інших факторів) до умов балансування на верстатах.
Практика показала, що ретельно врівноважене робоче колесо на верстаті необхідно додатково врівноважувати у власних опорах. Очевидно, що незадовільний вібраційний стан вентиляційних агрегатів при введенні в експлуатацію після монтажу або ремонту приводить до передчасного спрацювання устаткування. З іншої сторони транспортування рабочего колеса до балансувального верстата за багато кілометрів від промислового підприємства не виправдана з погляду тимчасових і фінансових витрат. Додаткове розбирання, ризик ушкодження робочого колеса при транспортуванні, усе це доводить ефективність зрівноважування на місці експлуатації у власних опорах.
Поява сучасної вібровимірювальної апаратури забезпечує можливість проведення динамічного балансування на місці експлуатації й зниження вібраційної навантаженості опор до припустимих меж.
Однієї з аксіом працездатного стану встаткування є робота механізмів з низьким рівнем вібрації. У цьому випадку знижується вплив цілого ряду руйнівних факторів, що впливають на підшипникові вузли механізму. При цьому збільшується довговічність підшипникових вузлів і механізму в цілому, забезпечується стабільна реалізація технологічного процесу, відповідно до заданих параметрів. Щодо вентиляторів і димососів, низький рівень вібрації багато в чому визначається врівноваженістю робочих коліс, вчасно проведеною балансуванням.
Наслідку роботи механізму з підвищеною вібрацією: руйнування підшипникових вузлів, посадкових місць підшипників, фундаментів, підвищена витрата електричної енергії для привода установки. У даній роботі розглядаються наслідки несвоєчасного балансування робочих коліс димососів і вентиляторів цехів металургійних підприємств.
Вібраційне обстеження вентиляторів доменного цеху показало, що основною причиною підвищеної вібрації є динамічна неврівноваженість робочих коліс. Ухвалене рішення – провести зрівноважування робочих коліс у власних опорах дозволило знизити загальний рівень вібрації 3…5 раз, до рівня 2,0…3,0 мм/із при роботі під навантаженням (малюнок 1). Це дозволило побільшати термін служби підшипників в 5…7 раз. Визначене, що для однотипних механізмів спостерігається істотний розкид динамічних коефіцієнтів впливу (більш 10 %), що визначає необхідність проведення балансування у власних опорах. Основними факторами, що впливають на розкид коефіцієнтів впливи є: нестабільність динамічних характеристик роторів; відхилення властивостей системи від лінійності; погрішності при установці пробних вантажів.
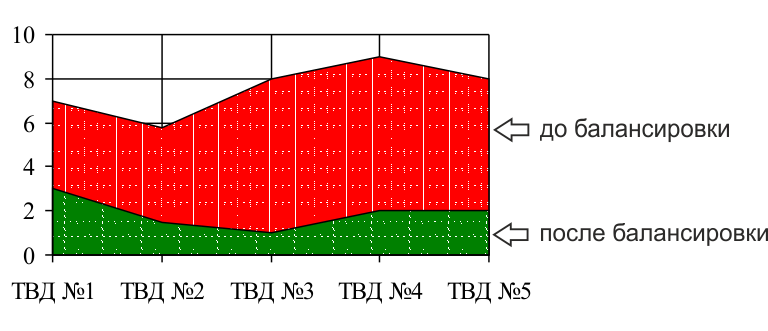
Малюнок 1 - Максимальні рівні вібрашвидкості (мм/с) підшипникових опор вентиляторів до й послі балансування
Серед причин виникнення дисбалансу робочих коліс димососів і вентиляторів слід виділити:
1. Нерівномірне зношування лопаток (малюнок 2), незважаючи на симетрію робочого колеса й значну частоту обертання. Причина даного явища може полягати у вибірковій випадковості процесу зношування, обумовленого зовнішніми факторами й внутрішніми властивостями матеріалу. Необхідно враховувати фактичні відхилення геометрії лопаток від проектного профілю.
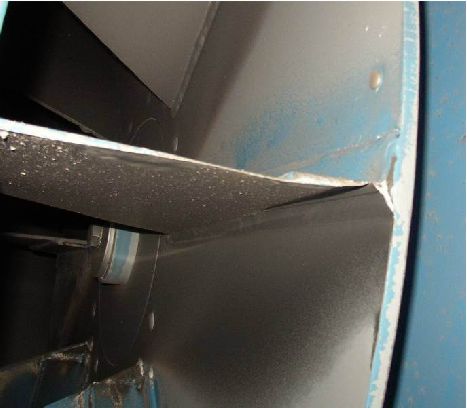 | |
а) | б) |
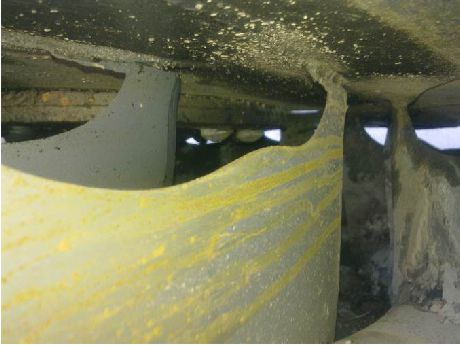 | |
в) | г) |
Малюнок 2 – Нерівномірне ерозійне зношування лопаток робочого колеса
Серед причин виникнення дисбалансу робочих коліс димососів і вентиляторів слід виділити:
1. Нерівномірне зношування лопаток (малюнок 2), незважаючи на симетрію робочого колеса й значну частоту обертання. Причина даного явища може полягати у вибірковій випадковості процесу зношування, обумовленого зовнішніми факторами й внутрішніми властивостями матеріалу. Необхідно враховувати фактичні відхилення геометрії лопаток від проектного профілю.
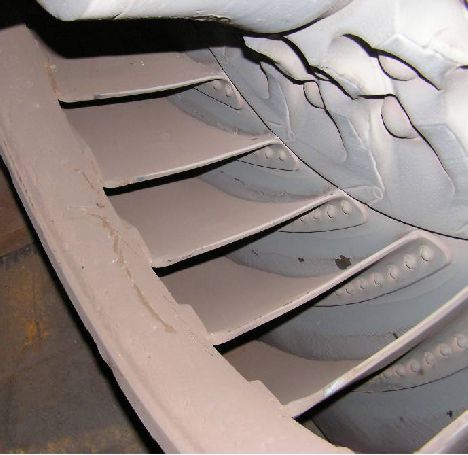 | |
а)
| б) |
Малюнок 3 – Налипання пилоподібних матеріалів на лопатки робочого колеса:
а) димосос аглофабрики; б) паровідсос МНЛЗ
3. Наслідку ремонту лопаток у робочих умовах на місці установки. Іноді дисбаланс може викликатися проявом початкових тріщин у матеріалі дисків і лопаток робочих коліс. Тому, випереджати балансування повинен ретельний візуальний огляд цілісності елементів робочого колеса (малюнок 4). Заварка виявлених тріщин не може забезпечити тривалу безвідмовну роботу механізму. Зварені шви служать концентраторами напруги й додатковими джерелами зародження тріщин. Рекомендується використовувати даний метод відновлення лише, у крайньому випадку, для забезпечення функціонування на короткому тимчасовому проміжку, що дозволяє продовжити експлуатацію до виготовлення й заміни робочого колеса.
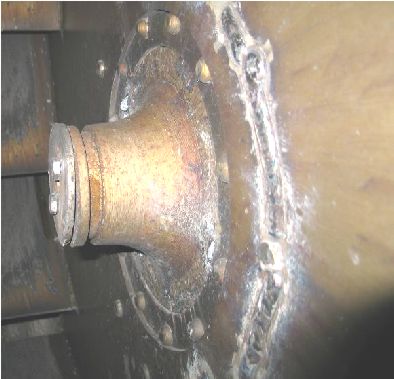 | |
а) | б) |
Малюнок 4 – Тріщини елементів робочих коліс:
а) основного диска; б) лопаток у місці кріплення
У роботі механізмів роторного типу важливу роль відіграють припустимі значення параметрів вібрації. Практичний досвід показав, що дотримання рекомендацій стандарту ДЕРЖСТАНДАРТ ИСО 10816-1-97 «Вібрація. Контроль стану машин за результатами вимірів вібрації на необертових частинах» щодо машин класу 1, дозволяє забезпечити тривалу експлуатацію димососів. Для оцінки технічного стану пропонується використовувати наступні значення й правила:
- значення віброшвидкості 1,8 мм/з, визначає границю функціонування встаткування без обмеження строків і бажаний рівень закінчення балансування робочого колеса у власних опорах;
- значення віброшвидкості в діапазоні 1,8…4,5 мм/з допускають роботу встаткування протягом тривалого періоду часу з періодичним контролем параметрів вібрації;
- значення віброшвидкості понад 4,5 мм/зі спостережувані протягом тривалого періоду часу (1…2 місяця) можуть привести до ушкоджень елементів устаткування;
- значення віброшвидкості в діапазоні 4,5…7,1 мм/з допускають роботу встаткування протягом 5…7 днів з наступною зупинкою на ремонт;
- значення віброшвидкості в діапазоні 7,1…11,2 мм/з допускають роботу встаткування протягом 1…2 днів з наступною зупинкою на ремонт;
- значення віброшвидкості понад 11,2 мм/з не допускаються й розглядаються як аварійні.
Аварійний стан розглядається як втрата контролю над технічним станом устаткування. Для оцінки технічного стану приводних електродвигунів використовується ГОСТ 20815-93 «Машини електричні обертові. Механічна вібрація деяких видів машин з висотою осі обертання 56 мм і вище. Вимір, оцінка й припустимі значення», що визначає значення віброшвидкості 2,8 мм/з як припустиме в процесі експлуатації. Слід зазначити, що запас міцності механізму дозволяє витримати й більш високі значення віброшвидкості, але це приводить до різкого зменшення довговічності елементів.
На жаль, установка вантажів, що компенсують, під час балансування, не дозволяє оцінити зниження довговічності підшипникових вузлів і підвищення енергетичних витрат при підвищеній вібрації димососів. Теоретичні розрахунки приводять до занижених значень втрат потужності на вібрацію[4, 5].
Додаткові сили, що діють на підшипникові опори, при неврівноваженому роторі, приводять до підвищення моменту опору обертанню вала вентилятора й до підвищення споживаної електроенергії. З'являються руйнівні сили, що діють на підшипникові опори й елементи механізму.
Оцінити ефективність зрівноважування роторів вентиляторів або додаткових ремонтних впливів по зниженню вібрації, в умовах експлуатації можливо проаналізувавши наступні дані.
Настановні параметри: тип механізму; потужність привода; напруга; частота обертання; маса; основні параметри робочого процесу.
Початкові параметри: віброшвидкість у контрольних точках (СКЗ у частотному діапазоні 10…1000 Гц); струм і напруга по фазах.
Виконані ремонтні впливи: значення встановленого пробного вантажу; виконане затягування нарізних сполучень; центрування.
Значення параметрів після виконаних впливів: віброшвидкість; струм і напруга по фазах.
У лабораторних умовах проведені дослідження зі зниження споживаної потужності двигуном вентилятора Д-3 у результаті зрівноважування ротора.
Результати експерименту №1.
Вентилятор ДН-6. Напруга 380 В. Частота обертання – 960 хв-1.
Початкова вібрація: вертикальна – 9,4 мм/з; осьова – 5,0 мм/с.
Струм по фазах: 3,9 А; 3,9 А; 3,9 А. Середнє значення – 3,9 А.
Вібрація після балансування: вертикальна – 2,2 мм/з; осьова – 1,8 мм/с.
Струм по фазах: 3,8 А; 3,6 А; 3,8 А. Середнє значення – 3,73 А.
Зниження параметрів вібрації: вертикальний напрямок – в 4, 27 рази; осьовий напрямок в 2, 78 рази.
Зниження струмових значень: (3,9 – 3,73)×100%3,73 = 4,55 %.
Результати експерименту №2.
Вентилятор ДН-6. Напруга 380 В. Частота обертання – 960 хв-1.
Початкова вібрація.
Крапка 1 – лобовий підшипник електродвигуна: вертикальна – 17,0 мм/з; горизонтальна – 15,3 мм/з; осьова – 2,1 мм/с. Радіус-Вектор – 22,9 мм/с.
Крапка 2 – вільний підшипник електродвигуна: вертикальна – 10,3 мм/з; горизонтальна – 10,6 мм/з; осьова – 2,2 мм/с.
Радіус-Вектор віброшвидкості – 14,9 мм/с.
Вібрація після балансування
Крапка 1: вертикальна – 2,8 мм/з; горизонтальна – 2,9 мм/з; осьова – 1,2 мм/с. Радіус-Вектор віброшвидкості – 4,2 мм/с.
Крапка 2: вертикальна – 1,4 мм/з; горизонтальна – 2,0 мм/з; осьова – 1,1 мм/с. Радіус-Вектор віброшвидкості – 2,7 мм/с.
Зниження параметрів вібрації.
Складові по крапці 1: вертикальна – в 6 раз; горизонтальна – в 5, 3 рази; осьова – в 1, 75 рази; радіус-вектор – в 5, 4 рази.
Складові по крапці 2: вертикальна – в 7, 4 рази; горизонтальна – в 5, 3 рази; осьова – в 2 рази, радіус-вектор – в 6, 2 рази.
Енергетичні показники.
До балансування Спожита потужність за 15 хвилин – 0,69 кВт. Максимальна потужність – 2,96 кВт. Мінімальна потужність – 2,49 кВт. Середня потужність – 2,74 кВт.
Після балансування Спожита потужність за 15 хвилин – 0,65 кВт. Максимальна потужність – 2,82 кВт. Мінімальна потужність – 2,43 кВт. Середня потужність – 2,59 кВт.
Зниження енергетичних показників Спожита потужність – (0,69 - 0,65)×100%/0,65 = 6,1 %. Максимальна потужність – (2,96 - 2,82)×100%/2,82 = 4,9 %. Мінімальна потужність – (2,49 - 2,43)×100%/2,43 = 2,5 %. Середня потужність – (2,74 - 2,59)/2,59×100% = 5,8 %.
Аналогічні результати були отримані у виробничих умовах при балансуванні вентилятора ВДН-12 нагрівальної тризонної методичної печі листопрокатного стану. Споживання електроенергії за 30 хвилин склало – 33,0 кВт, після балансування – 30,24 кВт. Зниження споживаної електроенергії в цьому випадку склало (33,0 - 30,24) ×100%/30,24 = 9,1 %.
віброшвидкість до балансування – 10,5 мм/з, після балансування – 4,5 мм/с. Зниження значень віброшвидкості – в 2, 3 рази.
Зниження споживаної потужності на 5% для одного 100 кВт двигуна вентилятора приведе до річної економії порядку 10 тис. гривень. Це може бути досягнуте в результаті балансування ротора й зниження вібраційних навантажень. Одночасно відбувається збільшення довговічності підшипників і зниження витрат на зупинку виробництва для проведення ремонтних робіт.
Одним з параметрів оцінки ефективності балансування є частота обертання вала димососа. Так, при балансуванні димососа ДН-26 зафіксоване збільшення частоти обертання електродвигуна АОД-630-8В1 послу установки коригувального вантажу й зниження віброшвидкості підшипникових опор. Віброшвидкість підшипникової опори до балансування: вертикальна – 4,4 мм/з; горизонтальна – 2,9 мм/с. Частота обертання до балансування – 745 про/хв. Віброшвидкість підшипникової опори після балансування: вертикальна – 2,1 мм/з; горизонтальна – 1,1 мм/с. Частота обертання після балансування – 747 про/хв.
Технічна характеристика асинхронного двигуна АОД-630-8В1: число пара полюсів – 8; синхронна частота обертання – 750 про/хв; номінальна потужність – 630 кВт; номінальний момент – 8130 Н/м; номінальна частота обертання -740 про/хв; МПУСК/МНОМ – 1,3; напруга – 6000 В; кпд – 0,948; cosφ = 0,79; коефіцієнт перевантаження – 2,3. Виходячи з механічної характеристики асинхронного двигуна АОД-630-8В1, збільшення частоти обертання на 2 про/хв можливо при зниженні крутного моменту на 1626 Н/м, що приводить до зниження споживаної потужності на 120 кВт. Це майже 20% від номінальної потужності.
Аналогічна залежність між частотою обертання й віброшвидкість зафіксована по асинхронних двигунах вентиляторів сушильних агрегатів під час проведення робіт з балансування (таблиця).
Таблиця – Значення віброшвидкості й частоти обертання двигунів вентиляторів
Амплітуда віброшвидкості складової оборотної
частоти, мм/з
|
Частота обертання, про/хв
|
2,6
|
2910
|
1,6
|
2906
|
5,0
|
2902
|
10,1
|
2894
|
13,1
|
2894
|
Залежність між частотою обертання й значенням віброшвидкості наведено на малюнку 5, там же зазначене рівняння лінії тренда й вірогідність апроксимації. Аналіз отриманих даних указує на можливість східчастої зміни частоти обертання при різних значеннях віброшвидкості. Так, значенням 10,1 мм/з і 13,1 мм/з відповідає одне значення частоти обертання – 2894 про/хв, а значенням 1,6 мм/з і 2,6 мм/з відповідають частоти 2906 про/хв і 2910 про/хв. Виходячи з отриманої залежності так само можна рекомендувати значення 1,8 мм/з і 4,5 мм/з як границі технічних станів.
Малюнок 5 - Залежність між частотою обертання й значенням віброшвидкості
У результаті проведених досліджень установлене.
1. Зрівноважування робочих коліс у власних опорах димососів металургійних агрегатів дозволяє забезпечити значне зниження споживаної енергії, побільшати термін служби підшипників.
2. Основними причинами зниження споживаної енергії є зменшення паразитних навантажень і зниження моменту опору в підшипникових опорах; зменшення вібраційних навантажень на елементи механізму.
3. Рекомендується для димососів і вентиляторів границею гарного стану (безвідносно до потужності двигуна) установити значення 1,8 мм/з, границею поганого стану визначити значення 4,5 мм/з.