Основне обладнання лінії гарячого цинкування (кількість обладнання і його габарити наведені, як приклад, вони можуть змінюватися в залежності від конкретних вимог).
Устаткування ділянки хімічної підготовки металоконструкцій цеху гарячого цинкування:
№
|
Найменування
|
кількість
|
Внутрішні габарити, мм
|
1
|
Ванна кислотного знежирення
|
2
|
3x1,8x13
|
2
|
Ванна травлення
|
7
|
3x1,8x13
|
3
|
Ванна промивки
|
2
|
3x1,8x13
|
4
|
Ванна флюсування
|
1
|
3x1,8x13
|
5
|
Ванна охолодження
|
1
|
3x1,8x13
|
Ванни хімічної підготовки цеху гарячого цинкування представляють собою сталеву конструкцію, з зовнішнім і внутрішнім спеціальним покриттям.
Всі ванни, крім ванни охолодження, оснащені автоматичною системою нагріву з бойлером. Автоматична система включає в себе систему контролю температури, в тому числі контролер температури, термопари з корпусами, теплообмінники.
Сушильна піч призначена для сушіння і попереднього нагріву виробів після флюсування перед зануренням деталей в розплав цинку.
Нагрівання сушильної печі здійснюється від газів горіння, що відходять від печі оцинкування. Передбачено додатковий нагрів пальником, що працює на природному газі. Контроль температури печі - автоматичний.
Транспортування траверс уздовж сушильної печі здійснюється ланцюговим конвеєром.
Піч цинкування горизонтального типу призначена для гарячого цинкування металоконструкцій методом занурення в розплав цинку.
Піч гарячого цинкування складається з:
-
печі гарячого цинкування;
-
ванни гарячого цинкування;
-
обладнання для вимірювання та регулювання температури;
-
установки збору білих димів;
-
установки рекуперації відпрацьованих газів.
Піч гарячого цинкування призначена для нагріву і підтримки робочої температури розплаву цинку в ванні. Піч являє собою металеву оболонку, яка містить ізолюючу кладку. Усередині оболонки знаходиться ванна і порожня порожнина між ванною і ізоляцією є камерою згоряння.
Ванна гарячого цинкування призначена для утримання розплавленого цинку при температурі до 480
0С. Ванна виготовлена з декількох секцій U образного сталевого профілю, зварених разом двостороннім швом. Матеріал корпусу ванни - сталь, з низьким вмістом вуглецю і кремнію, товщиною 50 мм. Ванна оцинкування вбудована в піч нагріву. Розмір ванни 12,5х1,6 м, глибина - 3 м, маса 47 т.
Температура ванни гарячого цинкування вимірюється за допомогою спеціальних датчиків (термопар) і передається терморегуляторам, керуючим запалюванням і відключенням рамп, що нагрівають. Система управляє температурою, як у зовнішній зоні (камері згоряння), так і у внутрішній зоні (ванна цинку).
Для уловлювання і відведення парів гарячого цинкування піч оснащена установкою витяжки та фільтрації газів.
Для забезпечення нагріву ванн хімічної підготовки служить установка рекуперації тепла відпрацьованих газів печі гарячого цинкування.
Транспортування траверс по всьому технологічному циклу гарячого цинкування здійснюється мостовими двох-візкового кранами.
Переміщення траверс між прольотами здійснюється спеціальними рейковими візками.
Устаткування ділянки хімічної підготовки
Для дотримання технологічного процесу гарячого цинкування на ділянці попередньої підготовки виробів необхідно здійснювати контроль за:
- температурою розчинів в ваннах;
-
рівнем розчинів в ваннах;
-
концентрацією розчинів.
Контроль і регулювання температур розчинів виконується автоматичною системою управління в межах певних параметрів. Вимірювання здійснюється за допомогою термопар. У разі виникнення будь-яких помилок система видає повідомлення на дисплей чергового поста, за усунення яких відповідає черговий оператор поста управління цеху гарячого цинкування.
Робочий рівень розчинів повинен витримуватися в межах 250 ÷ 300 мм від верхнього рівня ванн. Контроль за рівнем розчинів здійснюється на початку кожної зміни.
Контроль концентрації розчинів здійснюється лаборантом хім. лабораторії. Результати аналізів лаборант заносить на стенд в цеху, на підставі яких хімік-технолог цеху здійснює коригування розчинів. Результати аналізів на стенді оновлюються щодня.
Завантаження хімічних реактивів і долівку води в ванни до технологічного рівня, виконує спеціально призначений працівник цеху гарячого цинкування, що має допуск роботи з кислотою, на підставі даних розрахунків виконаних хіміком-технологом цеху і при його особистій присутності.
Піч гарячого цинкування
В процесі експлуатації печі гарячого цинкування необхідно виконувати наступні роботи:
Поточне обслуговування печі:
- Контроль рівня цинку в ванні;
- Чистка розплаву у ванні;
- Контроль температури розплаву цинку;
а
- Чистка дзеркала ванни від изгари і золкі.
Планово-профілактичні роботи по експлуатації печі:
- Чистка ванни від гартцинка;
- Чистка розплаву у ванні;
- Контроль рівня свинцевою подушки на дні ванни;
- Чистка бортів і внутрішніх стінок ванни;
- Контроль за станом вимірювальних приладів;
- Контроль за хімічним складом розплаву цинку;
- Огляд і ремонтні роботи оснащення, обладнання.
Контроль рівня цинку в ванні здійснюється на початку кожної зміни. Оптимальний рівень цинку 100 ÷ 150 мм від верхнього краю ванни. Заміри виконуються за допомогою лінійки або рулетки. При зниженні рівня до 150 мм, здійснюється дозавантаження злитків цинку в розплав. Завантаження цинку проводитися з бортів ванни. Для цього злитки цинку вручну викладаються по периметру ванни на бортах, потім оцінковщік за допомогою гака обережно, без сплесків, зіштовхує їх в розплав. При завантаженні значної кількості цинку (більше 5 тонн) проводиться чистка розплаву.
За контроль і регулювання температури розплаву цинку відповідає автоматична контрольно-вимірювальна система, що містить термопару, підключену до посту управління. Регулювання температури, в межах заданої (450 ° С), здійснюється автоматично.
Для перевірки точності приладів вимірювання та своєчасного регулювання температури, черговий оператор поста управління контролює температуру розплаву за показаннями другої, незалежної від автоматичної системи управління, термопари.
Чистка дзеркала ванни від жужелиці і золки проводиться при вивантаженні виробів з розплаву, для запобігання налипання оксидів на поверхні оцинкованих металоконструкцій. Крім того, дзеркало ванни необхідно чистити і перед зануренням виробів у розплав, у разі тривалого простою ванни і накопичення значної кількості золки і жужелиці на поверхні розплаву.
Щоденне чищення розплаву виконується оцінковщікамі один раз, на початку кожної зміни.
Раз в тиждень, піч цинкування зупиняється на проведення профілактичних робіт з метою виконання заходів перерахованих нижче.
Видалення гартцинка проводиться після оцинковки 300-400 т продукції. Товщина шару гартцинка не повинна перевищувати 100 мм, інакше значно зменшується глибина ванни, а що утворюється цинкове покриття буде шорстким, від захоплених зі дна і поверхні стінок, часток гартцинка. Чистка виконується за допомогою спеціального ковша, що підвішується на гак мостового крана.
Після видалення гартцинка, а також у міру забруднення розплаву ( при завантаженні цинку в кількості більш 5 тонн або з появою на поверхні виробів чорних пластівців бруду), необхідно робити чищення розплаву.
Вимірювання висоти свинцевої подушки проводиться в останню профілактику місяця після чищення гартцинка. Висота свинцевої подушки повинна підтримуватися на рівні 100 мм.
Чищення бортів і внутрішніх стінок ванни від налиплого цинку, гартцинка виконується за допомогою спеціальних пристроїв - шкребків. Внутрішні стінки ванни очищаються на глибину 200-250 мм від верхніх бортів ванни.
За роботою контрольно-вимірювальних приладів також необхідно стежити. Періодично необхідно проводити чищення корпусів термопар від налиплого цинку, виконувати очищення корпуса термопари при кожному чищенні гартцинка.
Хімічний аналіз розплаву цинку на зміст алюмінію, свинцю, заліза робить хім.лабораторія цеху гарячого цинкування, з реєстрацією даних у журналі.
У процесі профілактичних робіт, здійснюється огляд технологічного оснащення на предмет наявності ушкоджень і при необхідності направляється на ремонт або списується.
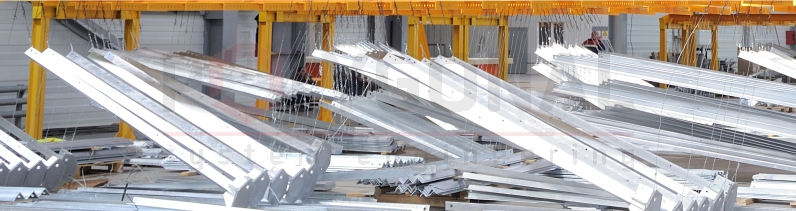
Технологічні операції гарячого цинкування
Металоконструкції, призначені для гарячого цинкування, послідовно піддаються наступним технологічним операціям:
навішення деталей на траверси; знежирення; травлення; промивання у воді; флюсування; сушка флюсу; гаряче цинкування; охолодження; контроль якості покриття; видача металоконструкцій на ділянку комплектації.
У якості технологічного оснащення для гарячого оцинкування деталей металоконструкцій застосовуються траверси, гаки, петлі із дроту й інші пристосування.
ТРАВЕРСУ – технологічне оснащення, призначена для навішення деталей під гаряче оцинкування. Деталі на одній і тій же траверсі проходять повний цикл без перезарядження: навішення, хім. підготовка, сушіння, оцинкування, охолодження, розрядка. Навішення деталей здійснюється на овальні отвори в куточках з нижньої сторони траверси.
Транспортування траверси між технологічними операціями здійснюється двовізковим мостовим краном.
ГАКИ призначені для навішення деталей на траверсу. Гаки різняться по довжині, діаметрі й за формою гнучкі – однобічні, двосторонні.
Діаметр гака залежить від маси, що навішується деталі й вибирається по таблиці вантажопідйомності гаків.
Крім гаків для навішення деталей на траверсу застосовується прокат сортовий сталевий гарячекатаний круглий ГОСТ 2590-2006 Ø6 мм, а так само дріт сталевий низьковуглецева загального призначення ГОСТ 3282-74 Ø3, Ø4 (далі по тексту - дріт). Залежно від маси, що навішується деталі дріт може бути вигнута у вигляді гака або у вигляді петлі.
Для зарядки й розрядки траверс використовуються спеціальні стійки висотою 2 м, призначені для втримання траверси на відповідній висоті в процесі навішення/розважування. Для навішення важких деталей використовується спеціальна стійка - гідропідйомник.
Усе технологічне оснащення підлягає періодичному огляду, для своєчасного виявлення пристосувань потребуючих ремонту. При огляді необхідно в першу чергу звертати увагу на стан зварених швів і несучих елементів конструкції (вушок, петель, гаків і інших несучих елементів конструкцій). У випадку виявлення зношування, більш ніж на 10%, оснащення необхідно відправити на ремонт.
Траверси, полоки з гаками підлягають обліку й реєстрації в журналі із присвоєнням реєстраційного номера. На всі пристосування повинні бути розроблені креслення із вказівкою припустимої вантажопідйомності. Дані про ремонти й випробування оснащення заносяться в реєстраційний журнал.
Для оцинкування, деталі на траверсу можуть бути навішені двома способами: у вертикальному положенні – за один кінець, або в горизонтальному положенні – за два кінці деталі.
Знежирення
На поверхні виробів, як правило, є жирові забруднення. Виріб може бути забруднене мастильними матеріалами двох типів:
- натуральні мінеральні масла;
- силіконові мастильні матеріали.
Наявність на поверхні виробів жирових забруднень викликає значні утруднення при гарячому цинкуванні, порушує адгезію цинкового покриття, приводить до утвору неоцинкованих ділянок або плям коричневого кольору.
З метою поліпшення якості цинкового покриття металоконструкції зазнають кислому хімічному знежиренню. Для готування розчину використовується знежирювач.
Для виконання знежирення траверсу з деталями занурюють у розчин. Тривалість процесу знежирення металоконструкцій при температурі 24-26°С становить 15-20 хвилин, при температурі 28-30°С – 10 хв. У процесі роботи контролюється кислотність розчину й температура.
Контроль і регулювання температури проводиться постійно автоматичною системою керування.
У процесі роботи на дно ванни випадає осад у вигляді дрібного піску. Його слід видаляти один раз у рік або коли рівень осаду на дні стає перешкодою для нормального занурення виробів у ванну знежирення. Питома вага й хімічна склад осаду може змінюватися залежно від типу жирів, внесених у ванну.
Для очищення піску слід перелити розчин у вільну ванну хім. підготовки, а потім механічним способом вилучити пісок із дна ванни. Очищення дна ванни здійснює працівник, призначений начальником цеху, відповідальним за виконання даних робіт. Пісок із дна ванни підлягає вивозу на полігон пром. відходів.
Після завершення процесу знежирення траверсу з деталями перевозять в одну з ванн травлення.
Травлення
На поверхні сталевих виробів можуть виникати оксиди різного состава й будови - іржа й окалина.
Іржа (Feo, Fe
2O
3 х nh
2O) утворюється в кисневмісному середовищі в присутності вологи при кімнатній температурі. Окалина на сталевих виробах звичайно утворюється в процесі їх виготовлення й при термічній обробці, по составу близька до оксидів заліза Feo-fe
3O
4- Fe
2O
3.
Видалення іржі й окалини проводиться хімічним методом (травленням) у водяному розчині соляної кислоти ( ГОСТ 857-95).
Час витримки у ванні травлення прямо пропорційно кількості іржі й окалини на поверхні, залежить від температури й концентрації травильного розчину й не залежить від товщини виробу. Травлення металоконструкцій проводиться до повного видалення іржі й окалини. Контроль якості поверхні – візуальний, для цього виробу періодично дістають з ванни для огляду. Тривалість травлення 20-90 хв.
Травлення металоконструкцій у соляній кислоті через можливий перетрава не можна робити без інгібіторів (сповільнювачів) кислотної корозії. Із застосуванням інгібітору досягається досить гарна якість травлення поверхні металоконструкцій.
Захист поверхні розчину від виділення пар соляної кислоти проводиться за допомогою додавання в розчин піноутворювачів.
Контроль і регулювання температури проводиться постійно автоматичною системою керування.
Після завершення процесу травлення траверсу з деталями перевозять у ванну промивання.
Промивання
Промивання здійснюється після травлення, перед переходом у ванну флюсовання. Промивання роблять шляхом 3-х кратного занурення деталей у ванну. Промивне середовище – вода. Основна мета промивання - видалення залишків травильного розчину, заліза і його з'єднань із поверхні виробу.
Залізо впливає на процес флюсовання:
- забруднює розчин флюсу, який вимагає періодичного відновлення;
- на поверхні оцинкованого виробу виникають «крихти»;
- у цинковому розплаві утворюється гартцинк: 1 грам заліза, що потрапив у цинковий розплав, утворює 40 грам гартцинка. Відповідно, досить 20 грамів заліза, щоб втратити 1 кг цинку у формі осаду.
Промивна вода може повторно використовуватися у ванні травлення, де залізо корисне: свіжий травильний розчин працює ефективно, тільки якщо в ньому є невелика кількість заліза.
На лінії хімічної підготовки чиста вода заливається тільки у ванни промивання, що скорочує її споживання.
Аналіз води на зміст соляної кислоти й заліза у ванні промивання виконується щодня. При досягненні концентрації заліза 4 г/л виконати повну або часткову заміну розчину.
Флюсовання
Добре протравлені й промиті металоконструкції надходять на заключну, підготовчу операцію – флюсовання
Флюсовання проводять для забезпечення правильної «реакції» з розплавленим цинком, для додаткового видалення солей і оксидів металів з поверхні виробу, не знятих у ванні промивання, а також з поверхні розплавленого цинку в місці занурення виробу й, крім того, для поліпшення змочування поверхні виробу розплавленим цинком шляхом зниження поверхневого натягу розплаву цинку. Летучі з'єднання, що утворюються при розкладанні флюсу, сприяють механічному видаленню забруднень на дзеркалі ванни й створюють нейтральну атмосферу в місці занурення виробів у розплав цинку.
У результаті флюсовання на поверхні сталевого виробу утворюється плівка солей (хлористого цинку Zncl
2 і хлористого амонію NH
4Cl), що запобігає окиснення аж до занурення в розплав цинку, де відбувається реакція між цинком і залізом. Соляна плівка здійснює подвійну дію:
- не допускає окиснення виробів на повітрі з моменту виходу з ванни травлення й до занурення у ванну цинкування;
- дозволяє регулювати товщину цинкового покриття (разом із двома іншими факторами: часом занурення й температурою цинкового розплаву).
У якості флюсу використана суміш із солей хлористого амонію - NH
4Cl і хлористого цинку - Zncl
2. Основну роль у такому флюсі відіграє хлористий амоній, тому що він є постачальником газоподібних хлоридів, що утворюються при розкладанні NH
4Cl при контакті з розплавленим цинком:
NH4Cl - NH3 + Hcl
Ця реакція йде в присутності вологи, яка завжди є на виробі. Волога сприяє розкладанню хлористих солей з утвором активної соляної кислоти. Хлористий водень Hcl взаємодіє з оксидом заліза Feo, цинку Zno і інших елементів, що присутні на дзеркалі ванни:
Feo + 2Hcl - Fecl2 + H2O
Zno + 2Hcl - Zncl2 + H2O
Більшість хлоридів, що утворюються (алюмінію, олова, сурми, Fecl
3) випаровується, тому що їхня температура кипіння нижче температури розплаву цинку.
Із хлоридом заліза Fecl
2 зв'язаний утвір гартцинка - небажаного продукту процесу цинкування.
При контакті з розплавленим цинком Fecl
2 відновлюється до заліза.
Fecl2 + Zn - Zncl2 + Fe
залізо, Що Утворювалося, взаємодіючи з рідким цинком, переходить у гартцинк, осідаючи на дно цинкової подушки (на шар свинцю). Це ще раз підтверджує необхідність гарного промивання після травлення.
Для поліпшення якості гарячого цинкування у флюс додають різні присадки. На поверхні металу солі хлористого цинку й хлористого амонію формують кристали. При наявності присадки кристали виходять більшими й розташовуються в одному напрямку, що робить більш щільної кристалічну соляну сітку на поверхні виробу й забезпечує більш надійний його захист від окиснення. При цьому оцинкований виріб виходить блискучим, скорочується витрата цинку й утвір золки. Добавка присадки виявляє особливий вплив і на «міжкристалічний шар» - ділянка взаємного проникнення цинку й заліза. Основна частина цинкового покриття на сталевому виробі представлена саме цим шаром, який значно товстіше поверхневого шару чистого цинку.
Тривалість процесу флюсовання 30-45 секунд, що відповідає одному зануренню в розчин флюсу.
Температура розчину флюсовання 40°С при використанні сушильної печі й 70°С без використання печі.
При досягненні концентрації солей заліза більш 6 г/л розчин флюсовання коректується автоматичною системою очищення флюсу. Принцип дії системи полягає в зниженні кислотності розчину й добуванні з нього розчиненого заліза. Для коректування рівня кислотності використовується водний аміак. Для добування розчиненого заліза його спочатку переводять у нерозчинний гідроокис тривалентного заліза, для чого в розчин додають пероксид водню, а потім за допомогою фільтрації виводять залізо із флюсового розчину.
Сушіння
Після ванни флюсовання траверсу з деталями переноситься в сушильну піч для прогріву й видалення залишків вологи. При цьому:
- у результаті випару води на поверхні формується сітка, що полягає із кристалів солей, що забезпечує захист від окиснення на повітрі;
- скорочується перепад температур між розплавом цинку й виробом, витягнутим з ванни флюсовання;
- виключається влучення води в розплавлений цинк.
Температура сушіння не повинна перевищувати 120°С. Час знаходження металоконструкцій у сушильній печі – до повного випару вологи з поверхні металу (10-60 хв).
Після завершення операції сушіння, траверсу з деталями перевозиться в піч цинкування.
Гаряче цинкування
Цинк - блакитнувато-сріблистий метал з температурою плавлення 419,5
0С и температурою кипіння 906+1
0С. Щільність твердого цинку 7,133 г/см3 ( при 20
0З), рідкого 6,66 г/см3 ( при 419,5
0С); отже, при плавленні цинку його обсяг збільшується. Технічно чистий цинк при звичайних температурах дуже тендітний, але при нагріванні до 100¸150
0З має гарну пластичність.
При дифузійному цинкуванні жидкофазним способом у розплаві цинку (гаряче цинкування) відбувається взаємодія сталі з розплавленим цинком, у результаті якого на поверхні сталевого виробу утворюються залізоцинкові з'єднання (фази). При цьому змінюється хімічний склад і структура поверхневого шару цинку.
Дифузійне цинкове покриття, отримане в розплаві цинку, складається з декількох залізоцинкових фаз, розташованих безпосередньо на основному металі, і шару цинку. Шар цинку, який по составу в основному відповідає розплаву, виникає при добуванні виробу з ванни цинкування. імовірність утвору тих або інших шарів залізоцинкових з'єднань у покритті багато в чому залежить від режиму цинкування, состава й структури металу, а також від состава розплаву цинку.
Товщина покриття для сталей при однаковому стані їх поверхні залежить від тривалості гарячого цинкування, температури розплаву цинку і його состава, а також від швидкості добування цинкового покриття.
Гаряче цинкування проводиться в розплаві цинку марки ЦВО або ЦВ ГОСТ 3640-94.
Стадії гарячого цинкування
Виробничий процес гарячого цинкування ділиться за часом на стадії:
- занурення виробу в розплав цинку;
- витримка до повного википан флюсу й до вирівнювання температури виробу й розплаву цинку;
- вивантаження виробу з розплаву цинку;
- охолодження виробу.
Для одержання пластичного, підвищеної корозійної стійкості й гарного виду цинкового покриття, а також для затримки утвору проміжних фаз (залізоцинкових сплавів) цинковий розплав легується алюмінієм, у якості якого використовується евтектичний сплав цинку й алюмінію марки ЦА-10 ГОСТ 21438 в обсязі 0,05-0,2 % від ваги цинку. Зміст алюмінію в розплаві повинне бути в межах до 0,05%. Алюміній створює тугоплавку плівку, що сприяє зменшенню вигару цинку із дзеркала ванни.
При завантаженні ЦА-10 у ванну, необхідно забезпечити його плавлення максимально близько до поверхні розплаву цинку.
Контроль змісту алюмінію в розплаві виконується щодня. Результати аналізу заносяться в реєстраційний журнал і на дошку цеху.
Для осадження гартцинка на дно ванни, у розплав необхідно додавати свинець. Свинець розплавляється в цинку до 1%-1,3%, понад це, свинець осаджується на дно ванни, формуючи шар свинцю, що полягає з 98% свинцю й 2% цинку. Шар свинцю на дні ванни взаємодіє з жужелицею, перешкоджаючи прикипанню жужелиці до дна ванни. Необхідно підтримувати шар свинцю до 100 мм. Додавання свинцю також збільшує плинність цинку. Рівень свинцю повинен перевіряться 1 раз на місяць. Свинець додається у ванну за допомогою крана у вигляді злитків, покладених у кошик, при цьому, необхідно забезпечити рівномірний розподіл свинцю по дну ванни. Після додавання свинцю, ванна цинкування повинна відстоятися 40 хвилин.
Температурні режими
Робоча температура розплаву, при якій відбувається оцинкування металоконструкцій 450°С. Контроль і регулювання температури в межах заданої здійснюється автоматично через термопару, підключену до PLC системі керування піччю гарячого цинкування.
Для запобігання зниження температури розплаву цинку нижче технологічного рівня не рекомендується занурювати в розплав більш 15 тонн металоконструкцій протягом години.
Підвищення температури вище зазначеної скорочує термін служби ванни.
Автоматична система контролю над температурою дублюється переносною термопарою.
Охолодження
Покриті цинком виробу зазнають охолодженню у ванні охолодження з метою зниження температури й збереження блиску покриття. Вода не проточна. Охолодження проводиться шляхом 1-кратного занурення. Температура води у ванні охолодження не повинна перевищувати 80°С. У міру випару вода додається у ванну.
Допускається охолодження деталей на повітрі.
Розважування траверси після оцинкування
Після охолодження деталей, траверсу перевозять мостовим краном на ділянку розважування.
Охолоджену траверсу встановлюють на стійки під розважування. Висота стійок 2 метра. Вибір висоти стійок під розважування здійснюється залежно від габаритів деталей.
Великогабаритні зварені вузли (масою більш 60 кг) знімають із траверси, установленої на гідропідйомнику.
Розважування деталей на дроті. Для знімання деталей із траверси, дріт зрізують за допомогою ножиців по металу або гострозубців.
Вільні від деталей траверси передаються на ділянку навішення.
Контроль якості
Звільнені від пристосувань деталі укладаються на стелажі в пачки й оглядаються працівниками ВТК із метою контролю якості цинкового покриття. Можливі дефекти гарячого цинкування й причини їх виникнення розглядаються в наступній статті.