Основное оборудование линии горячего цинкования (количество оборудования и его габариты приведены, как пример, они могут изменяться в зависимости от конкретных требований).
Оборудование участка химической подготовки металлоконструкций цеха горячего цинкования:
№
|
Наименование
|
количество
|
Внутренние габариты, мм
|
1
|
Ванна
кислотного обезжиривания
|
2
|
3x1,8x13
|
2
|
Ванна
травления
|
7
|
3x1,8x13
|
3
|
Ванна
промывки
|
2
|
3x1,8x13
|
4
|
Ванна
флюсования
|
1
|
3x1,8x13
|
5
|
Ванна
охлаждения
|
1
|
3x1,8x13
|
Ванны химической подготовки цеха горячего цинкования представляют собой стальную конструкцию, с наружным и внутренним специальным покрытием.
Все ванны, кроме ванны охлаждения, оснащены автоматической системой нагрева с бойлером. Автоматическая система включает в себя систему контроля температуры, в том числе контроллер температуры, термопары с корпусами, теплообменники.
Сушильная печь предназначена для сушки и предварительного нагрева изделий после флюсования перед погружением деталей в расплав цинка.
Нагрев сушильной печи осуществляется от отходящих газов горения печи оцинкования. Предусмотрен дополнительный нагрев горелкой, работающей на природном газе. Контроль температуры печи – автоматический.
Транспортировка траверс вдоль сушильной печи осуществляется цепным конвейером.
Печь цинкования горизонтального типа предназначена для горячего цинкования металлоконструкций методом погружения в расплав цинка.
Печь горячего цинкования состоит из:
-
печи горячего цинкования;
-
ванны горячего цинкования;
-
оборудования для измерения и регулирования температуры;
-
установки сбора белых дымов;
-
установки рекуперации отработанных газов.
Печь горячего цинкования предназначена для нагрева и поддержания рабочей температуры расплава цинка в ванне. Печь представляет собой металлическую оболочку, содержащую изолирующую кладку. Внутри оболочки находится ванна и пустая полость между ванной и изоляцией является камерой сгорания.
Ванна горячего цинкования предназначена для содержания расплавленного цинка при температуре до 480
0С. Ванна изготовлена из нескольких секций U образного стального профиля, сваренных вместе двухсторонним швом. Материал корпуса ванны - сталь, с низким содержанием углерода и кремния, толщиной 50 мм. Ванна оцинкования встроена в печь многопламенного нагрева. Размер ванны 12,5х1,6 м, глубина – 3 м, масса 47 т.
Температура ванны горячего цинкования измеряется с помощью специальных датчиков (термопар) и передается терморегуляторам, управляющим зажиганием и отключением нагревающих рамп. Система управляет температурой, как в наружной зоне (камере сгорания), так и во внутренней зоне (ванна цинка).
Для улавливания и отвода паров горячего цинкования печь оснащена установкой вытяжки и фильтрации газов.
Для обеспечения нагрева ванн химической подготовки служит установка рекуперации тепла отработанных газов печи горячего цинкования.
Транспортировка траверс по всему технологическому циклу горячей оцинковки осуществляется мостовыми двух-тележечными кранами.
Перемещение траверс между пролетами осуществляется специальными рельсовыми тележками.
Оборудование участка химической подготовки
Для соблюдения технологического процесса горячего цинкования на участке предварительной подготовки изделий необходимо осуществлять контроль за:
- температурой растворов в ваннах;
-
уровнем растворов в ваннах;
-
концентрацией растворов.
Контроль и регулировка температур растворов выполняется автоматической системой управления в пределах определенных параметров. Измерение осуществляется с помощью термопар. В случае возникновения каких либо ошибок система выдает сообщение на дисплей дежурного поста, за устранение которых отвечает дежурный оператор поста управления цеха горячего цинкования.
Рабочий уровень растворов должен выдерживаться в пределах 250÷300 мм от верхнего уровня ванн. Контроль за уровнем растворов осуществляется в начале каждой смены.
Контроль концентрации растворов осуществляется лаборантом хим. лаборатории. Результаты анализов лаборант заносит на стенд в цехе, на основании которых химик-технолог цеха производит корректировку растворов. Результаты анализов на стенде обновляются ежедневно.
Загрузку химических реактивов и доливку воды в ванны до технологического уровня, выполняет специально назначенный работник цеха горячего цинкования, имеющий допуск работы с кислотой, на основании данных расчетов выполненных химиком-технологом цеха и при его личном присутствии.
Печь горячего цинкования
В процессе эксплуатации печи горячего цинкования необходимо выполнять следующие работы:
Текущее обслуживание печи:
- Контроль уровня цинка в ванне;
- Чистка расплава в ванне;
- Контроль температуры расплава цинка;
- Чистка зеркала ванны от изгари и золки.
Планово-профилактические работы по эксплуатации печи:
- Чистка ванны от гартцинка;
- Чистка расплава в ванне;
- Контроль уровня свинцовой подушки на дне ванны;
- Чистка бортов и внутренних стенок ванны;
- Контроль за состоянием измерительных приборов;
- Контроль за химическим составом расплава цинка;
- Осмотр и ремонтные работы оснастки, оборудования.
Контроль уровня цинка в ванне осуществляется в начале каждой смены. Оптимальный уровень цинка 100÷150 мм от верхней кромки ванны. Замеры выполняются с помощью линейки или рулетки. При понижении уровня до 150 мм, осуществляется дозагрузка слитков цинка в расплав. Загрузка цинка производиться с бортов ванны. Для этого слитки цинка вручную выкладываются по периметру ванны на бортах, затем оцинковщик с помощью крюка осторожно, без всплесков, сталкивает их в расплав. При загрузке значительного количества цинка (более 5 тонн) производится чистка расплава.
За контроль и регулировку температуры расплава цинка отвечает автоматическая контрольно-измерительная система, содержащая термопару, подключенную к посту управления. Регулировка температуры, в пределах заданной (450°С), осуществляется автоматически.
Для проверки точности приборов измерения и своевременной регулировки температуры, дежурный оператор поста управления контролирует температуру расплава по показаниям второй, независимой от автоматической системы управления, термопары.
Чистка зеркала ванны от изгари и золки производится при выгрузке изделий из расплава, для предотвращения налипания окислов на поверхности оцинкованных металлоконструкций. Кроме того, зеркало ванны необходимо чистить и перед погружением изделий в расплав, в случае длительного простоя ванны и накопления значительного количества золки и изгари на поверхности расплава.
Ежедневная чистка расплава выполняется оцинковщиками один раз, в начале каждой смены.
Раз в неделю, печь цинкования останавливается на проведение профилактических работ с целью выполнения мероприятий перечисленных ниже.
Удаление гартцинка производится после оцинковки 300-400 т продукции. Толщина слоя гартцинка не должна превышать 100 мм, иначе значительно уменьшается глубина ванны, а образующееся цинковое покрытие будет шероховатым, от захваченных со дна и поверхности стенок, частиц гартцинка. Чистка выполняется с помощью специального ковша, подвешиваемого на крюк мостового крана.
После удаления гартцинка, а также по мере загрязнения расплава (при загрузке цинка в количестве более 5 тонн или при появлении на поверхности изделий черных хлопьев грязи), необходимо производить чистку расплава.
Измерение высоты свинцовой подушки производится в последнюю профилактику месяца после чистки гартцинка. Высота свинцовой подушки должна поддерживаться на уровне 100 мм.
Чистка бортов и внутренних стенок ванны от налипшего цинка, гартцинка выполняется с помощью специальных приспособлений - скребков. Внутренние стенки ванны очищаются на глубину 200-250 мм от верхних бортов ванны.
За работой контрольно-измерительных приборов также необходимо следить. Периодически необходимо проводить чистку корпусов термопар от налипшего цинка, выполнять очистку корпуса термопары при каждой чистке гартцинка.
Химический анализ расплава цинка на содержание алюминия, свинца, железа производит хим.лаборатория цеха горячего цинкования, с регистрацией данных в журнале.
В процессе профилактических работ, осуществляется осмотр технологической оснастки на предмет наличия повреждений и при необходимости направляется на ремонт или списывается.
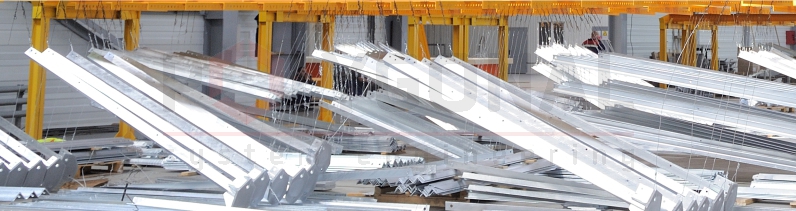
Технологические операции горячего цинкования
Металлоконструкции, предназначенные для горячего цинкования, последовательно подвергаются следующим технологическим операциям:
навеска деталей на траверсы; обезжиривание; травление; промывка в воде; флюсование; сушка флюса; горячее цинкование; охлаждение; контроль качества покрытия; выдача металлоконструкций на участок комплектации.
В качестве технологической оснастки для горячей оцинковки деталей металлоконструкций применяются траверсы, крюки, петли из проволоки и другие приспособления.
ТРАВЕРСА – технологическая оснастка, предназначенная для навески деталей под горячую оцинковку. Детали на одной и той же траверсе проходят полный цикл без перезарядки: навеска, хим. подготовка, сушка, оцинковка, охлаждение, разрядка. Навеска деталей осуществляется на овальные отверстия в уголках с нижней стороны траверсы.
Транспортировка траверсы между технологическими операциями осуществляется двухтележечным мостовым краном.
КРЮКИ предназначены для навески деталей на траверсу. Крюки различаются по длине, диаметру и по форме гибки – односторонние, двухсторонние.
Диаметр крюка зависит от массы навешиваемой детали и выбирается по таблице грузоподъемности крюков.
Кроме крюков для навески деталей на траверсу применяется прокат сортовой стальной горячекатаный круглый ГОСТ 2590-2006 Ø6 мм, а так же проволока стальная низкоуглеродистая общего назначения ГОСТ 3282-74 Ø3, Ø4 (далее по тексту - проволока). В зависимости от массы навешиваемой детали проволока может быть изогнута в виде крюка или в виде петли.
Для зарядки и разрядки траверс используются специальные стойки высотой 2 м, предназначенные для удержания траверсы на соответствующей высоте в процессе навески/развески. Для навески тяжелых деталей используется специальная стойка - гидроподъемник.
Вся технологическая оснастка подлежит периодическому осмотру, для своевременного выявления приспособлений требующих ремонта. При осмотре необходимо в первую очередь обращать внимание на состояние сварных швов и несущих элементов конструкции (проушин, петель, крюков и других несущих элементов конструкций). В случае обнаружения износа, более чем на 10%, оснастку необходимо отправить на ремонт.
Траверсы, полоки с крюками подлежат учету и регистрации в журнале с присвоением регистрационного номера. На все приспособления должны быть разработаны чертежи с указанием допустимой грузоподъемности. Данные о ремонтах и испытаниях оснастки заносятся в регистрационный журнал.
Для оцинковки, детали на траверсу могут быть навешены двумя способами: в вертикальном положении – за один конец, либо в горизонтальном положении – за два конца детали.
Обезжиривание
На поверхности изделий, как правило, имеются жировые загрязнения. Изделие может быть загрязнено смазочными материалами двух типов:
- натуральные минеральные масла;
- силиконовые смазочные материалы.
Наличие на поверхности изделий жировых загрязнений вызывает значительные затруднения при горячем цинковании, нарушает адгезию цинкового покрытия, приводит к образованию неоцинкованных участков или пятен коричневого цвета.
С целью улучшения качества цинкового покрытия металлоконструкции подвергаются кислому химическому обезжириванию. Для приготовления раствора используется обезжириватель.
Для выполнения обезжиривания траверсу с деталями погружают в раствор. Продолжительность процесса обезжиривания металлоконструкций при температуре 24-26°С составляет 15-20 минут, при температуре 28-30°С – 10 мин. В процессе работы контролируется кислотность раствора и температура.
Контроль и регулировка температуры производится постоянно автоматической системой управления.
В процессе работы на дно ванны выпадает осадок в виде мелкого песка. Его следует удалять один раз в год или когда уровень осадка на дне становится помехой для нормального погружения изделий в ванну обезжиривания. Удельный вес и химический состав осадка может изменяться в зависимости от типа жиров, вносимых в ванну.
Для очистки песка следует перелить раствор в свободную ванну хим. подготовки, а затем механическим способом удалить песок со дна ванны. Очистку дна ванны осуществляет работник, назначенный начальником цеха, ответственным за выполнение данных работ. Песок со дна ванны подлежит вывозу на полигон пром. отходов.
После завершения процесса обезжиривания траверсу с деталями перевозят в одну из ванн травления.
Травление
На поверхности стальных изделий могут возникать оксиды различного состава и строения - ржавчина и окалина.
Ржавчина (FeO, Fe
2O
3 х nH
2O) образуется в кислородосодержащей среде в присутствии влаги при комнатной температуре. Окалина на стальных изделиях обычно образуется в процессе их изготовления и при термической обработке, по составу близка к оксидам железа FeO-Fe
3O
4- Fe
2O
3.
Удаление ржавчины и окалины производится химическим методом (травлением) в водном растворе соляной кислоты (ГОСТ 857-95).
Время выдержки в ванне травления прямо пропорционально количеству ржавчины и окалины на поверхности, зависит от температуры и концентрации травильного раствора и не зависит от толщины изделия. Травление металлоконструкций производится до полного удаления ржавчины и окалины. Контроль качества поверхности – визуальный, для этого изделия периодически извлекаются из ванны для осмотра. Продолжительность травления 20-90 мин.
Травление металлоконструкций в соляной кислоте из-за возможного перетрава нельзя производить без ингибиторов (замедлителей) кислотной коррозии. С применением ингибитора достигается достаточно хорошее качество травления поверхности металлоконструкций.
Защита поверхности раствора от выделения паров соляной кислоты производится при помощи добавления в раствор пенообразователей.
Контроль и регулировка температуры производится постоянно автоматической системой управления.
После завершения процесса травления траверсу с деталями перевозят в ванну промывки.
Промывка
Промывка осуществляется после травления, перед переходом в ванну флюсования. Промывку производят путем 2-3-х кратного окунания деталей в ванну. Промывочная среда – вода. Основная цель промывки - удаление остатков травильного раствора, железа и его соединений с поверхности изделия.
Железо оказывает отрицательное воздействие на процесс флюсования:
- загрязняет раствор флюса, который требует периодического восстановления;
- на поверхности оцинкованного изделия возникают «крошки»;
- в цинковом расплаве образуется гартцинк: 1 грамм железа, попавшего в цинковый расплав, образует 40 грамм гартцинка. Соответственно, достаточно 20 граммов железа, чтобы потерять 1 кг цинка в форме осадка.
Промывочная вода может повторно использоваться в ванне травления, где железо полезно: свежий травильный раствор работает эффективно, только если в нем есть небольшое количество железа.
На линии химической подготовки чистая вода заливается только в ванны промывки, что сокращает ее потребление.
Анализ воды на содержание соляной кислоты и железа в ванне промывки выполняется ежедневно. При достижении концентрации железа 4 г/л выполнить полную или частичную замену раствора.
Флюсование
Хорошо протравленные и промытые металлоконструкции поступают на заключительную, подготовительную операцию – флюсование
Флюсование проводят для обеспечения правильной «реакции» с расплавленным цинком, для дополнительного удаления солей и оксидов металлов с поверхности цинкуемого изделия, не снятых в ванне промывки, а также с поверхности расплавленного цинка в месте погружения изделия и, кроме того, для улучшения смачивания поверхности изделия расплавленным цинком путем снижения поверхностного натяжения расплава цинка. Летучие соединения, образующиеся при разложении флюса, способствуют механическому удалению загрязнений на зеркале ванны и создают нейтральную атмосферу в месте погружения изделий в расплав цинка.
В результате флюсования на поверхности стального изделия образуется пленка солей (хлористого цинка ZnCl
2 и хлористого аммония NH
4Cl), предотвращающая окисление вплоть до погружения в расплав цинка, где происходит реакция между цинком и железом. Соляная пленка осуществляет двойное действие:
- не допускает окисления изделий на воздухе с момента выхода из ванны травления и до погружения в ванну цинкования;
- позволяет регулировать толщину цинкового покрытия (вместе с двумя другими факторами: временем погружения и температурой цинкового расплава).
В качестве флюса использована смесь из солей хлористого аммония - NH
4Cl и хлористого цинка - ZnCl
2. Основную роль в таком флюсе играет хлористый аммоний, т.к. он является поставщиком газообразных хлоридов, образующихся при разложении NH
4Cl при контакте с расплавленным цинком:
NH4Cl - NH3 + HCl
Эта реакция идет в присутствии влаги, которая всегда имеется на изделии. Влага способствует разложению хлористых солей с образованием активной соляной кислоты. Хлористый водород HCl взаимодействует с оксидом железа FeO, цинка ZnO и других элементов, присутствующих на зеркале ванны:
FeO + 2HCl - FeCl2 + H2O
ZnO + 2HCl - ZnCl2 + H2O
Большинство образующихся хлоридов (алюминия, олова, сурьмы, FeCl
3) испаряется, т.к. их температура кипения ниже температуры расплава цинка.
С хлоридом железа FeCl
2 связано образование гартцинка - нежелательного продукта процесса цинкования.
При контакте с расплавленным цинком FeCl
2 восстанавливается до железа.
FeCl2 + Zn - ZnCl2 + Fe
Образовавшееся железо, взаимодействуя с жидким цинком, переходит в гартцинк, оседая на дно цинковой подушки (на слой свинца). Это еще раз подтверждает необходимость хорошей промывки после травления.
Для улучшения качества горячего цинкования во флюс добавляют различные присадки. На поверхности металла соли хлористого цинка и хлористого аммония формируют кристаллы. При наличии присадки кристаллы получаются более крупными и располагаются в одном направлении, что делает более плотной кристаллическую соляную сетку на поверхности изделия и обеспечивает более надежную его защиту от окисления. При этом оцинкованное изделие получается блестящим, сокращается расход цинка и образование золки. Добавка присадки оказывает особое воздействие и на «межкристаллический слой» - участок взаимного проникновения цинка и железа. Основная часть цинкового покрытия на стальном изделии представлена именно этим слоем, который значительно толще поверхностного слоя чистого цинка.
Продолжительность процесса флюсования 30-45 секунд, что соответствует одному окунанию в раствор флюса.
Температура раствора флюсования 40°С при использовании сушильной печи и 70°С без использования печи.
При достижении концентрации солей железа более 6 г/л раствор флюсования корректируется автоматической системой очистки флюса. Принцип действия системы заключается в снижении кислотности раствора и извлечении из него растворенного железа. Для корректировки уровня кислотности используется водный аммиак. Для извлечения растворенного железа его сначала переводят в нерастворимую гидроокись трехвалентного железа, для чего в раствор добавляют пероксид водорода, а затем посредством фильтрации выводят железо из флюсового раствора.
Сушка
После ванны флюсования траверса с деталями переносится в сушильную печь для прогрева и удаления остатков влаги. При этом:
- в результате испарения воды на поверхности формируется состоящая из кристаллов солей сетка, обеспечивающая защиту от окисления на воздухе;
- сокращается перепад температур между расплавом цинка и изделием, извлеченным из ванны флюсования;
- исключается попадание воды в расплавленный цинк.
Температура сушки не должна превышать 120°С. Время нахождения металлоконструкций в сушильной печи – до полного испарения влаги с поверхности металла (10-60 мин).
После завершения операции сушки, траверса с деталями перевозится в печь цинкования.
Горячее цинкование
Цинк - голубовато-серебристый металл с температурой плавления 419,5
0С и температурой кипения 906+1
0С. Плотность твердого цинка 7,133 г/см3 (при 20
0С), жидкого 6,66 г/см3 (при 419,5
0С); следовательно, при плавлении цинка его объем увеличивается. Технически чистый цинк при обычных температурах очень хрупкий, но при нагреве до 100¸150
0С обладает хорошей пластичностью.
При диффузионном цинковании жидкофазным способом в расплаве цинка (горячее цинкование) происходит взаимодействие стали с расплавленным цинком, в результате которого на поверхности стального изделия образуются железоцинковые соединения (фазы). При этом изменяется химический состав и структура поверхностного слоя цинка.
Диффузионное цинковое покрытие, полученное в расплаве цинка, состоит из нескольких железоцинковых фаз, расположенных непосредственно на основном металле, и слоя цинка. Слой цинка, который по составу в основном соответствует расплаву, возникает при извлечении изделия из ванны цинкования. вероятность образования тех или иных слоев железоцинковых соединений в покрытии во многом зависит от режима цинкования, состава и структуры цинкуемого металла, а также от состава расплава цинка.
Толщина покрытия для сталей при одинаковом состоянии их поверхности зависит от продолжительности горячего цинкования, температуры расплава цинка и его состава, а также от скорости извлечения цинкового покрытия.
Горячее цинкование производится в расплаве цинка марки ЦВО или ЦВ ГОСТ 3640-94.
Стадии горячего цинкования
Производственный процесс горячего цинкования делится по времени на стадии:
- погружение изделия в расплав цинка;
- выдержка до полного выкипания флюса и до выравнивания температуры изделия и расплава цинка;
- выгрузка изделия из расплава цинка;
- охлаждение изделия.
Для получения пластичного, повышенной коррозионной стойкости и хорошего вида цинкового покрытия, а также для замедления образования промежуточных фаз (железоцинковых сплавов) цинковый расплав легируется алюминием, в качестве которого используется эвтектический сплав цинка и алюминия марки ЦА-10 ГОСТ 21438 в объеме 0,05-0,2 % от веса цинка. Содержание алюминия в расплаве должно быть в пределах до 0,05%. Алюминий создает тугоплавкую пленку, что способствует уменьшению угара цинка с зеркала ванны.
При загрузке ЦА-10 в ванну, необходимо обеспечить его плавление максимально близко к поверхности расплава цинка.
Контроль содержания алюминия в расплаве выполняется ежедневно. Результаты анализа заносятся в регистрационный журнал и на доску цеха.
Для осаждения гартцинка на дно ванны, в расплав необходимо добавлять свинец. Свинец расплавляется в цинке до 1%-1,3%, свыше этого, свинец осаждается на дно ванны, формируя слой свинца, состоящий из 98% свинца и 2% цинка. Слой свинца на дне ванны взаимодействует с изгарью, препятствуя прикипанию изгари ко дну ванны. Необходимо поддерживать слой свинца до 100 мм. Добавление свинца также увеличивает текучесть цинка. Уровень свинца должен проверятся 1 раз в месяц. Свинец добавляется в ванну с помощью крана в виде слитков, уложенных в корзину, при этом, необходимо обеспечить равномерное распределение свинца по дну ванны. После добавления свинца, ванна цинкования должна отстояться 40 минут.
Температурные режимы
Рабочая температура расплава, при которой происходит оцинковка металлоконструкций 450°С. Контроль и регулировка температуры в пределах заданной осуществляется автоматически через термопару, подключенную к PLC системе управления печью горячего цинкования.
Для предотвращения понижения температуры расплава цинка ниже технологического уровня не рекомендуется погружать в расплав более 15 тонн металлоконструкций в течение часа.
Повышение температуры выше указанной сокращает срок службы ванны.
Автоматическая система контроля за температурой дублируется переносной термопарой.
Охлаждение
Покрытые цинком изделия подвергаются охлаждению в ванне охлаждения с целью снижения температуры и сохранения блеска покрытия. Вода не проточная. Охлаждение производится путем 1-кратного погружения. Температура воды в ванне охлаждения не должна превышать 80°С. По мере испарения вода добавляется в ванну.
Допускается охлаждение деталей на воздухе.
Развеска траверсы после оцинковки
После охлаждения деталей, траверсу перевозят мостовым краном на участок развески.
Охлажденную траверсу устанавливают на стойки под развеску. Высота стоек 2 метра. Выбор высоты стоек под развеску осуществляется в зависимости от габаритов навешенных деталей.
Крупногабаритные сварные узлы (массой более 60 кг) снимают с траверсы, установленной на гидроподъемнике.
Развеска деталей на проволоке. Для съема деталей с траверсы, проволоку срезают с помощью ножниц по металлу или кусачек.
Свободные от деталей траверсы передаются на участок навески.
Контроль качества
Освобожденные от приспособлений детали укладываются на стеллажи в пачки и осматриваются работниками ОТК с целью контроля качества цинкового покрытия. Возможные дефекты горячего цинкования и причины их возникновения рассматриваются в следующей статье.